Putting the Pieces Together
This week was spent further optimising the design of the Faraday Cage. Small changes were made to reduce the overall mass of the cage, and thus reduce material costs. The main changes have been in the top plate, where any of the unnecessary material has been removed, leaving only the interfaces for the bolts connecting the cage and the neutraliser. I’ve also added the hole grids to the bottom of the cage.
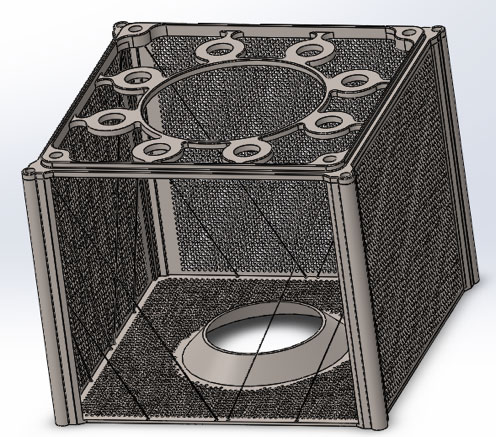
We have also started to piece together the overall assembly this week, including ancillary items such as nuts, bolts, and spacers. It is important to consider all these pieces in the assembly to ensure that all the components will fit together correctly when it is made. We had some further challenges to consider here.
Firstly, the neutraliser must be electrically isolated from the Faraday Cage. We will achieve this by using ceramic bushes, which will sit like sleeves over the bolts. These will prevent physical contact between the bolts and the Faraday Cage. Ceramic was chosen as it does not conduct electricity, and is also suitable for use in a vacuum. You can see the ceramic bushes in the full assembly, sat between the top of the neutraliser and the Faraday Cage:
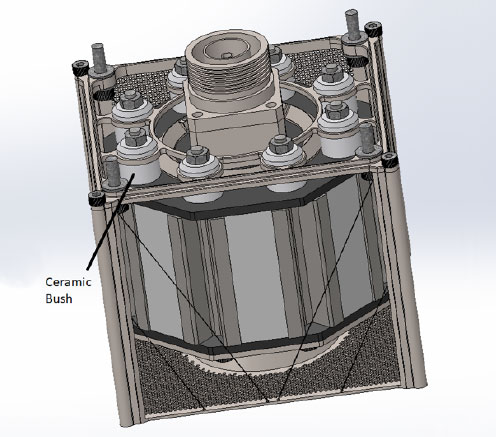
Secondly, we need to connect the entire assembly to a test interface plate, which also needs to be electrically isolated from our neutraliser. To do this, I’ve added some more holes to the top of the Faraday Cage, through which we will secure bolts to this plate. These can be seen in the assembly image above as the bolts which are pointing upwards. We will then use a PTFE ‘spacer’ to insulate the bolt from the test plate. A full mock-up of this should be ready in the next two weeks.
We will be holding our critical design review in a week’s time, and afterwards we can hopefully send everything off to be manufactured!
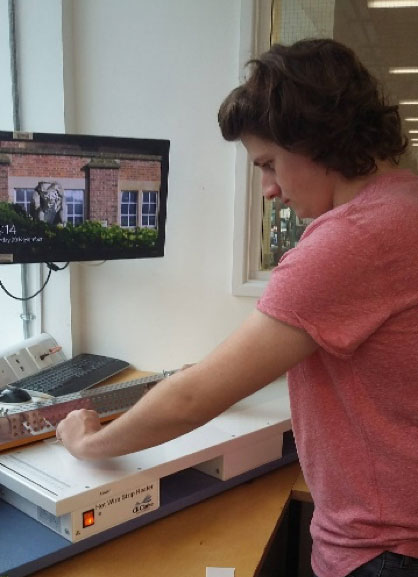
My experiments with PTFE this week were a mixed bag. I took a PTFE sheet to the heat-strip bending machine, but it was not accurate enough to produce the shape we required.
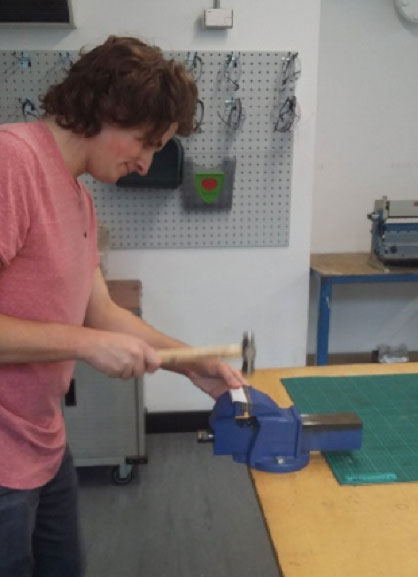
However, I noticed that the sheet was quite flexible itself (as it is only 1mm thick), and I was able to use a hammer and a clamp to crudely shape it.
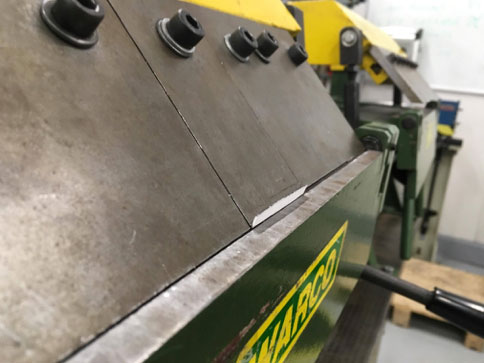
Although the hammering method did not bring optimal results, it did inspire me to try and use a folding machine to create the shape we needed. The folding machine clamps the sheet of PTFE in place, and folds it along a line. This worked much more effectively,
Marcus Collier-Wright