Preemptive Problem Solving
As our critical design review approaches at the end of the week, the group has started to move our focus away from optimising every small aspect of the design. Instead we are now working to solve the practical challenges which will arise from the neutraliser manufacture, assembly, and operation.
Our main concern is that the presence of plasma in the neutraliser chamber could cause a layer of metal to build up on the microwave antenna. This antenna must be electrically isolated from any other metal parts to prevent the transmission of microwaves to other parts of the neutraliser. To prevent this, we have devised a ceramic “shield” which stops the plasma from “seeing” the antenna when it passes into the iron yoke. The shield is formed of two parts, one of which is bolted to the yoke, and the other of which is secured by screws through the yoke column, as can be seen in the cross-sectional view below. The maze-like pattern is to prevent any plasma from reaching the part of the ceramic which is in contact with both the antenna and the yoke.
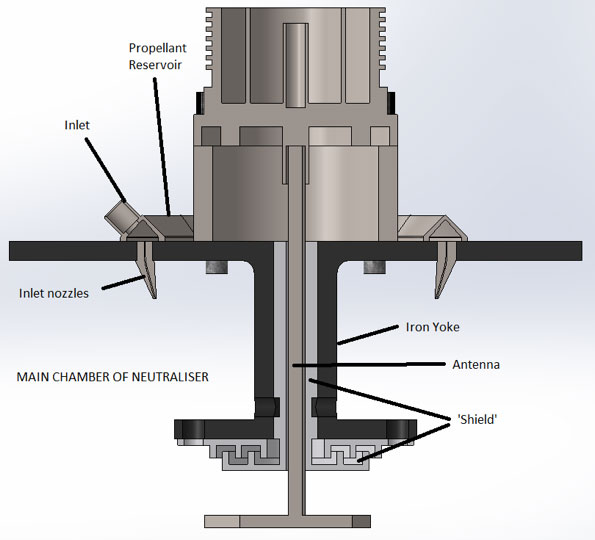
In the picture above you can also see the propellant reservoir (the ring structure on top of the yoke). The propellant enters this through the inlet on the left and sits in this reservoir, passing through the inlet nozzles to enter the main chamber of the neutraliser.
There have also been some further improvements to the Faraday Cage. The backplate design has changed, as we will need to find space to connect propellant tubes to the neutraliser. As such, we have removed 4 of the main bolts holding the neutraliser to improve accessibility inside the Faraday Cage. The support struts of the cage have also been thickened to improve their performance, and to ease the manufacturing process.
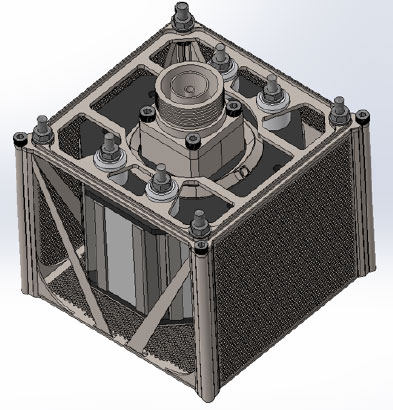
A lot of time this week has also been spent figuring out how some of the components will be made. Although we are using 3D stainless steel printing wherever possible, we can’t do this for all of our components. In particular, the iron yoke and the ceramic shielding provide tough manufacturing challenges. For the iron, we need to source our own supply of the material and after the yoke has been machined it will need to undergo special heat treatments to bring out its strong magnetic properties. The ceramic shield components will require specialist manufacture due to the challenging nature of machining ceramic. We are hoping to have some of these issues addressed by the end of the week!
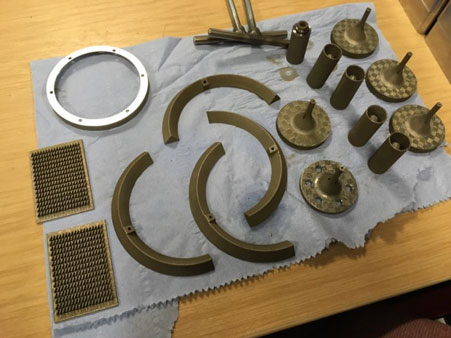
When visiting the University manufacturing centre this week I noticed some familiar looking components. The 4 semi-circular rings in the picture are parts of the ion thruster propellant system, designed by a PhD student we are working with. We will be using a similar design on our neutraliser, so it was really cool to see them in real life! There are also a few other interesting parts, all produced by the 3D printer, showing how easy it can be to make some of these things!
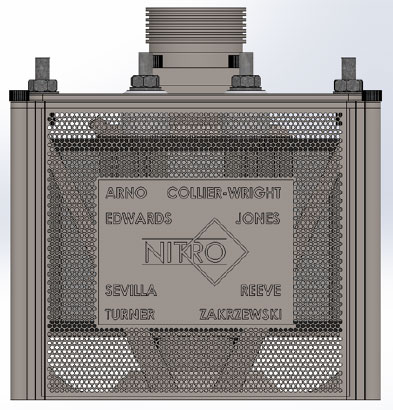
Finally, I’ve found some time to add a small cosmetic enhancement to our assembly: A plaque with the group members names and the project logo on it!
Marcus Collier-Wright