After a slower period of work on the group project, with Christmas and exams, Marcus returns to tell us about how the manufacture of the neutraliser is progressing.
A lot has happened since my last update. The design of the iron yoke/antenna assembly has changed yet again. Designing the yoke in two parts, as previously planned, would waste a lot of our iron, and eat into our allocated technician time. Furthermore, our supervisor was very keen for us to use a threaded connection between the antennas and the coaxial port. We have therefore reverted the iron yoke design to a single piece component. Although this will make assembling and disassembling the neutraliser much easier, we will need to machine down part of the coaxial port so that it will fit our antennas. As part of this redesign, we have had to enlarge the yoke tunnel in order to accommodate this part of the port.
We have been making great progress on the manufacturing front. So far, the 3 antenna designs have been manufactured (although only 2 of these were printed, as it turned out to be cheaper and quicker to machine the L-shape antenna by traditional methods). The stems of the antennas have already been threaded by the rest of the team.
The antenna shield has also been manufactured. Like the L-shape antenna, it was made via traditional methods.
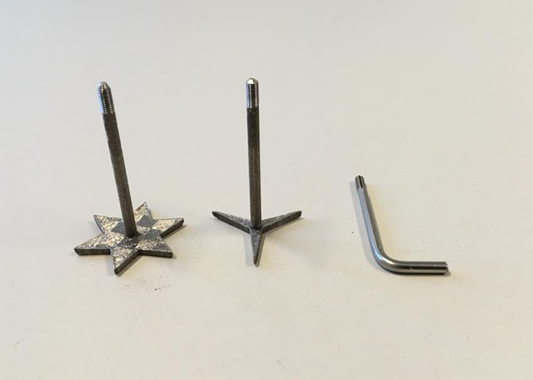
The antennas.
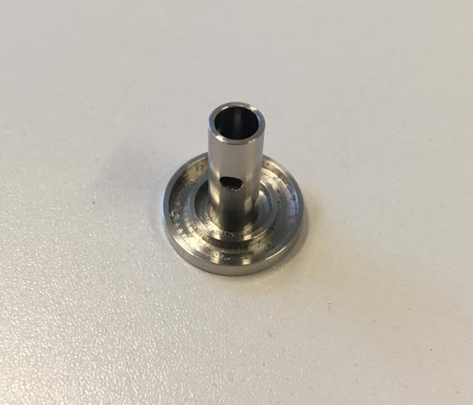
The antenna shield.
I’ve been spending a lot of time in the workshop working on our PTFE rods. We need one to sit in between the shield and the antenna, as well several rods which will connect the neutraliser and thruster assemblies to the test interface plate. To manufacture these to our specific requirements, I used a lathe to drill holes in the rods and to machine them down to the correct diameter. Here’s some pics of me using the lathe and attempting to thread the antennas.
Having successfully manufactured our PTFE insulating rod, I was able to piece together our first sub-assembly: The antenna, antenna shield, and insulating rod.
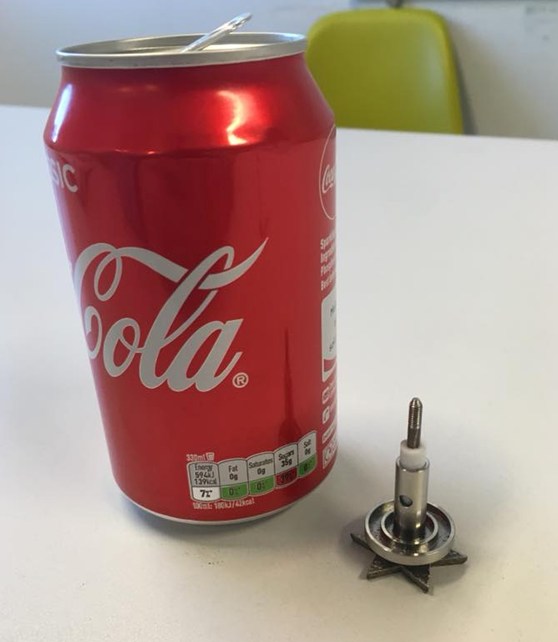
And here it is with a coke can for scale. It’s very small!!
We’ve also had a couple of our inlet nozzles printed. With some great difficulty, we were able to put a thread on these, although we’re concerned that the 0.2mm hole through the nozzle has not been printed accurately. As a backup, we will also print a version of the nozzles with a 0.5mm hole.
Our orifice and reservoir plates are nearing completion, so hopefully I’ll be able to show those off next week!
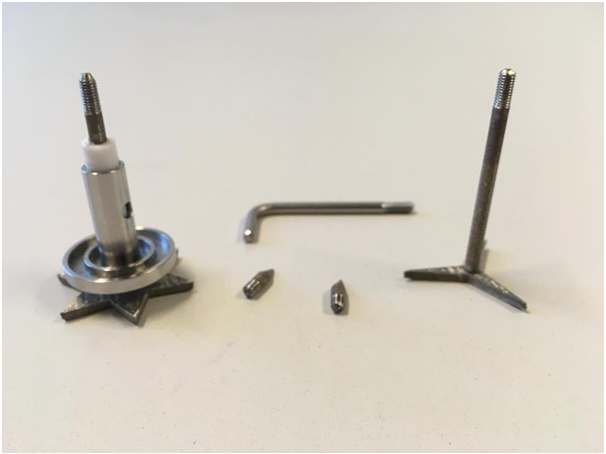
And finally, here’s a family photo of all our manufactured parts!
Marcus Collier-Wright