As more and more pieces are manufactured, Marcus’ design steadily becomes a reality.
We have continued to make timely progress on the manufacture of our neutraliser. Last week, one of our key components was delivered by the university manufacturing centre – the neutraliser backplate:
The backplate is especially vital as it provides the structural “anchor point” for the rest of the neutraliser components, and interfaces to the test support equipment in the vacuum chamber. The first order of business was to make sure that the backplate fitted together with the components we had already manufactured. It turned out that the main holes on the backplate were too small to accommodate the ceramic spacers, so I had to drill them out to a bigger size.
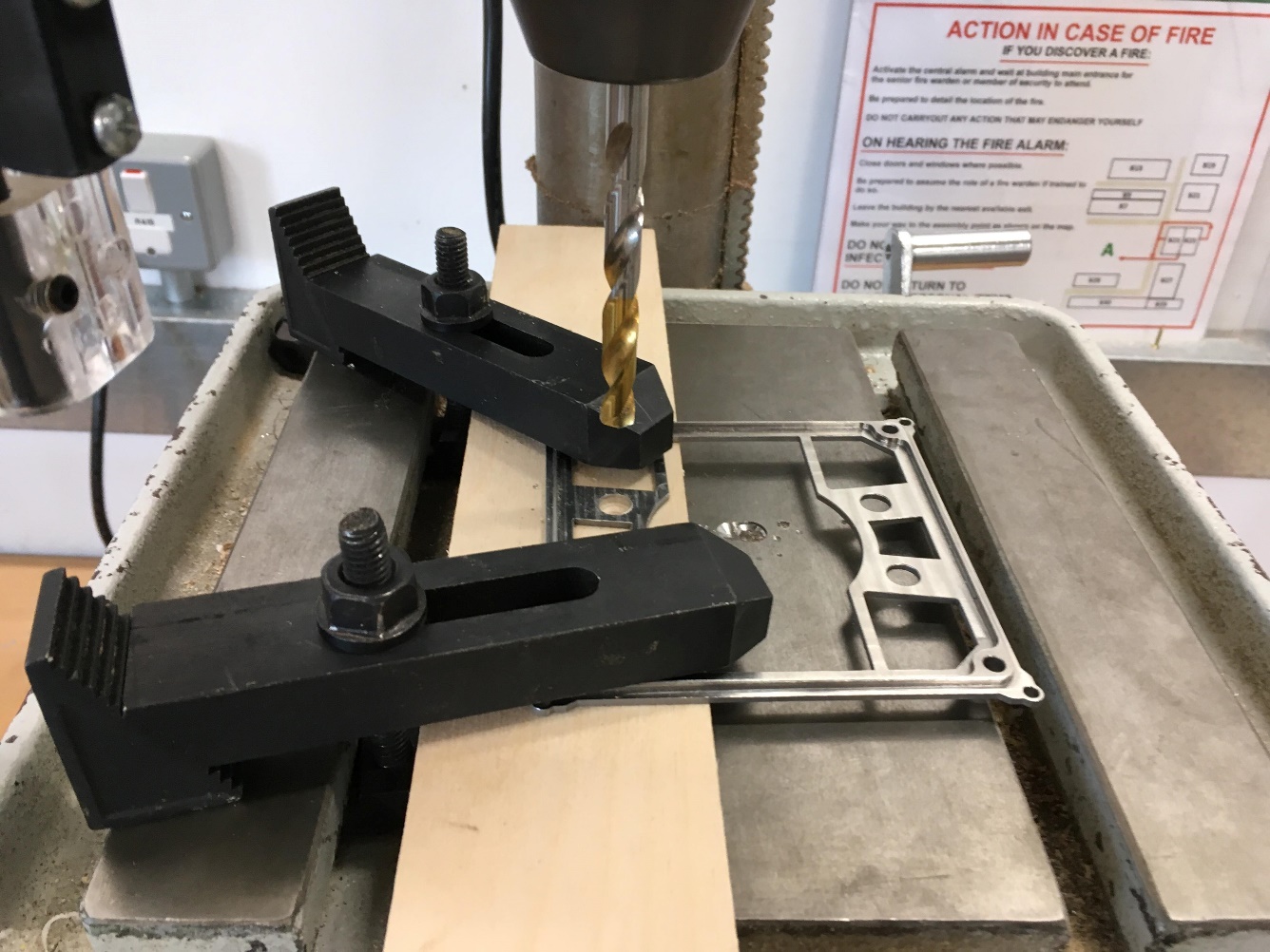
Having done this, I was able to assemble the backplate with the reservoir plate and ceramic spacers.
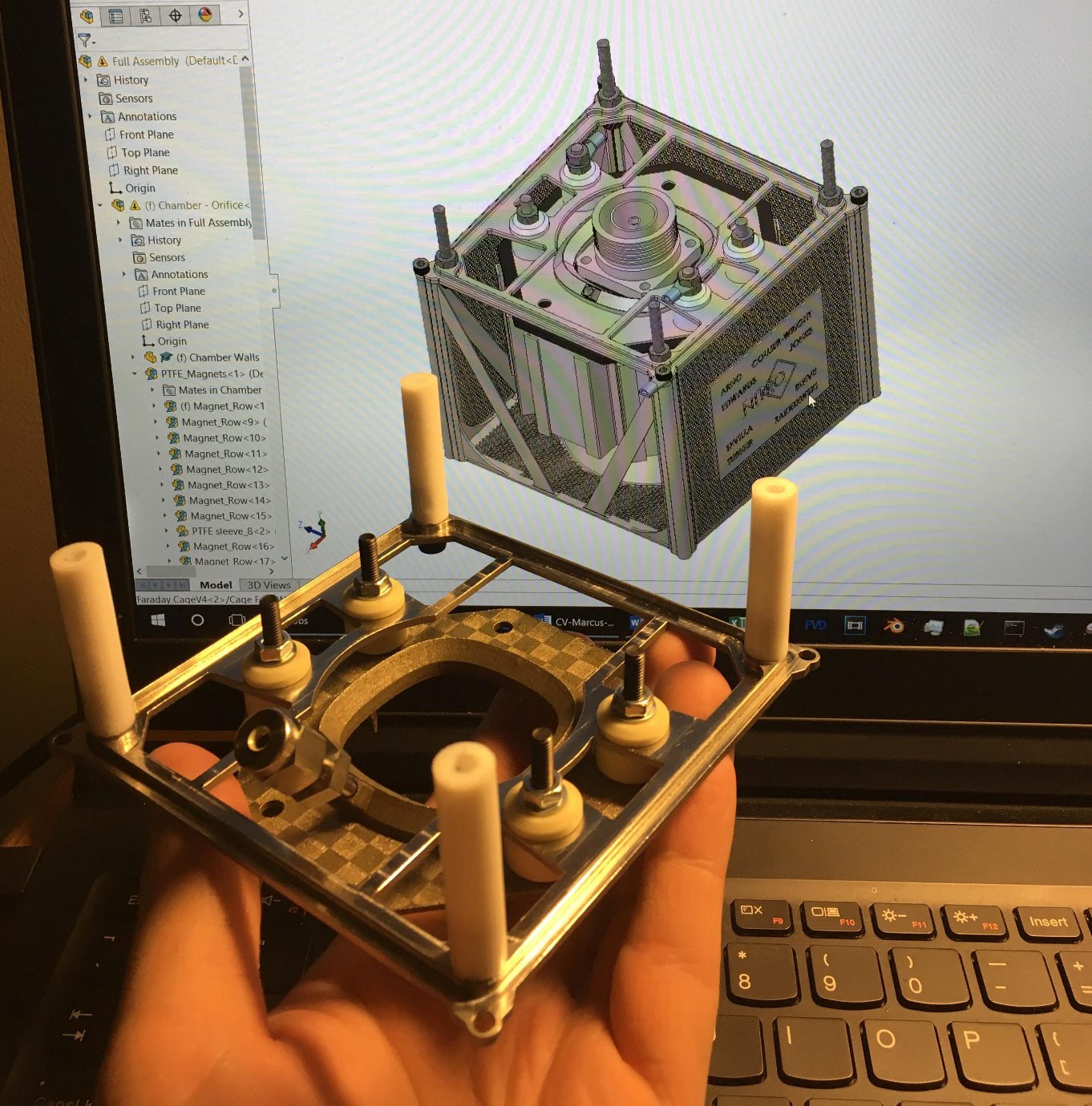
Everything now fits together nicely, and the ceramic spacers have worked exactly as designed. In this picture, you can see how we have progressed from design to reality. This journey is one of the things that I enjoy most about engineering!
Now that we had the backplate, we were able to check how well it integrates with the thruster test interface plate. The interface plate has been designed by the PhD student who is working on the thruster. It will allow us to mount the thruster and neutraliser together on the plate so that we can test them simultaneously. Fortunately, the two parts fit together perfectly! They are being held together by the PTFE rods which we manufactured earlier. These isolate the components from the interface plate, while providing a good structural support for the neutraliser.
Here are some pictures of the interface plate with our neutraliser components attached. The large octagonal space in the centre will be occupied by the thruster, while the other square section is for another type of electric thruster.
Finally, I can share a sneak peak of some new components. Our neutraliser chamber and one of our cage faces have been printed! They were made over the weekend, although the manufacturing centre still needs to separate them from the printer plate before we can use them. Nevertheless, its exciting that our final few components are almost ready!

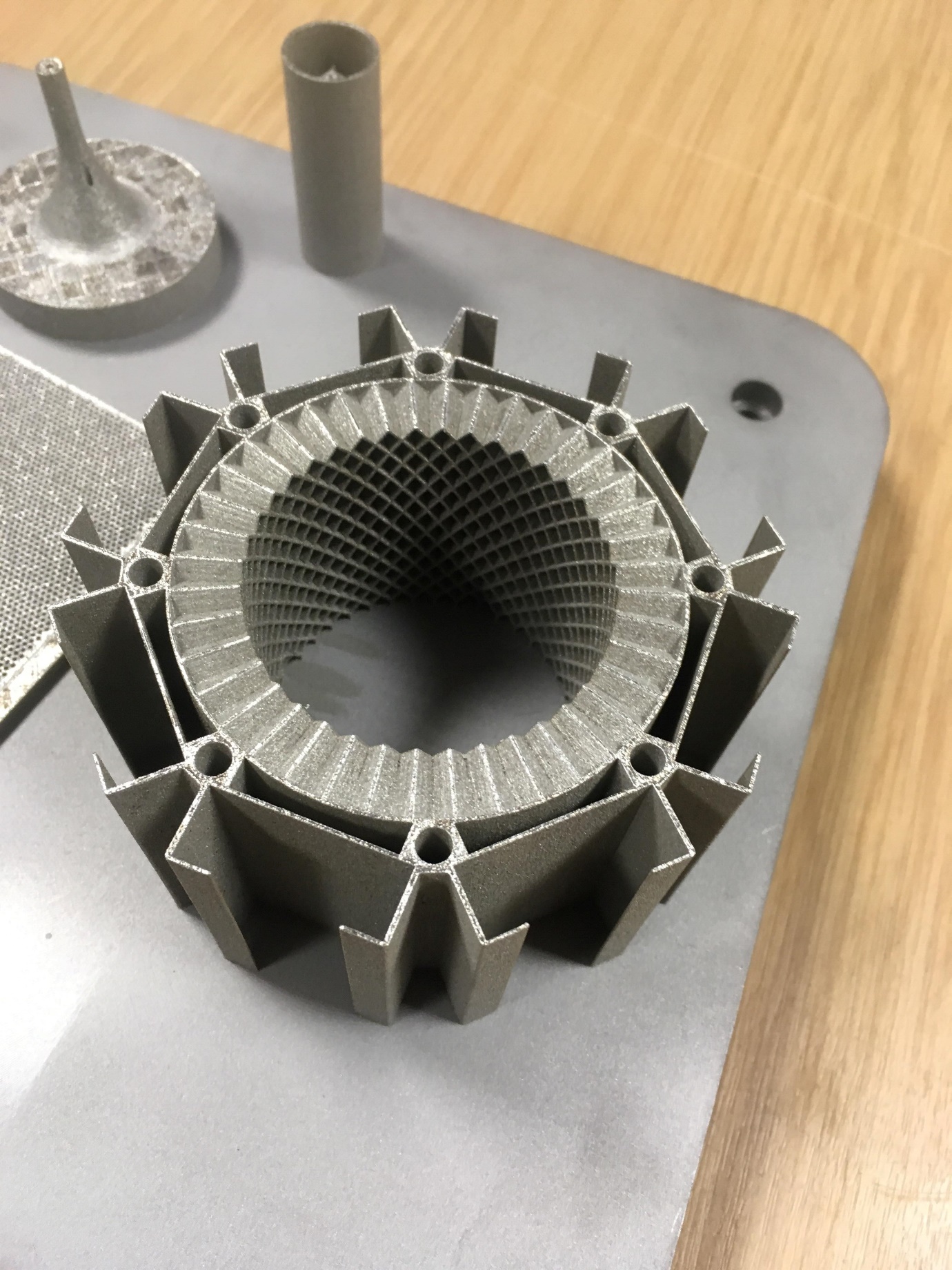
Marcus Collier-Wright